Formula 1 (F1) has been an early adopter of emerging technologies since its inception, and 3D printing has been no exception. 3D printing’s ability to quickly produce complex, lightweight, and robust structures has helped the technology become an integral part of the manufacturing process within the motorsport.
Additive manufacturing (AM), more commonly known as 3D printing, has been part of Formula 1 for many decades. Renault F1 bought its first 3D printer in 1998, however, the technology was not widely used until the mid-2010s.
3D printing’s low-volume production currently prevents the technology from being adopted in mass manufacturing. However, Formula 1 does not require mass production. At any one time, Formula 1 teams only work on two cars, making 3D printing a perfect fit for manufacturing in motorsport. Given the rapid iteration required of teams during the development phase, it is not surprising that 3D printing has been widely adopted throughout the sport.
Historically, 3D printing has been used in Formula 1 for prototyping, as 3D computer-aided design (CAD) software—a program used to blueprint 3D printed structures—provides a fast way to alter the intricate designs of wind tunnel components to better understand the aerodynamic properties of cars. The Alpine F1 team has admitted to prototyping 70% of the bodywork on its car.
Today, most Formula 1 teams have partnerships with leading 3D hardware and software manufacturers. For instance, Alpha Romeo ORLEN F1 works with Additive Industries, McLaren Racing with Stratasys, Alpine F1 with 3D Systems, and so on.
3D technologies in Formula 1
Fused deposition modeling (FDM), stereolithography (SLA), and bed power fusion are the most used 3D printing technologies in Formula 1.
How well do you really know your competitors?
Access the most comprehensive Company Profiles on the market, powered by GlobalData. Save hours of research. Gain competitive edge.
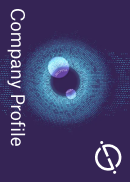
Thank you!
Your download email will arrive shortly
Not ready to buy yet? Download a free sample
We are confident about the unique quality of our Company Profiles. However, we want you to make the most beneficial decision for your business, so we offer a free sample that you can download by submitting the below form
By GlobalData- FDM is an extrusion-based technology. The solid material is forced through a nozzle, much like an automated version of a hot glue gun. Layer by layer a 3D structure is formed.
- SLA is a resin-based technology. The 3D printer starts with a container full of photopolymer liquid. The printer selectively hardens the liquid by exposing it to a focused beam of radiation. Layer by layer, a 3D structure is lifted from the liquid resin.
- Bed power fusion uses a pool of metal or polymer powder as its building material. A focused energy source, such as a laser, supplies intense heat to specific localized spots and melts or sinters the powder together to form a 3D structure.
FDM and SLA are cheaper technologies, while bed power fusion printers are more expensive, but provide high-precision and high-strength parts and do not require post-processing treatments.
The future of 3D printing in F1
Teams predominantly use 3D printing technologies for prototyping and other R&D processes; however, we are starting to see the technology being used in end-use parts, including exterior body parts, hydraulics management parts, and engine components. The Alpha Romeo ORLEN F1 team has partnered with Additive Industries to produce end-use aerodynamic components for its cars. Earlier this year, 3D-printed sensors were also spotted on Scuderia Ferrari’s race cars.
For low production volumes, 3D printing is a more economical and sustainable way of producing parts, due to the small amount of material used and the negligible amounts of waste produced compared to traditional manufacturing. According to GlobalData, the weight of 3D printed parts can be reduced by up to 93% in some cases, reducing the carbon footprint by up to 95%. However, the technology does not intend to replace traditional manufacturing. It instead seeks to complement existing production procedures. The budget price cap introduced in 2021 to Formula 1 will incentivize greater adoption of 3D printing in end-use manufacturing. Advancements in more robust, high-temperature materials will lower the cost and diversify the potential applications of 3D printing in motorsport.
Related Company Profiles
Stratasys Ltd
3D Systems Corp