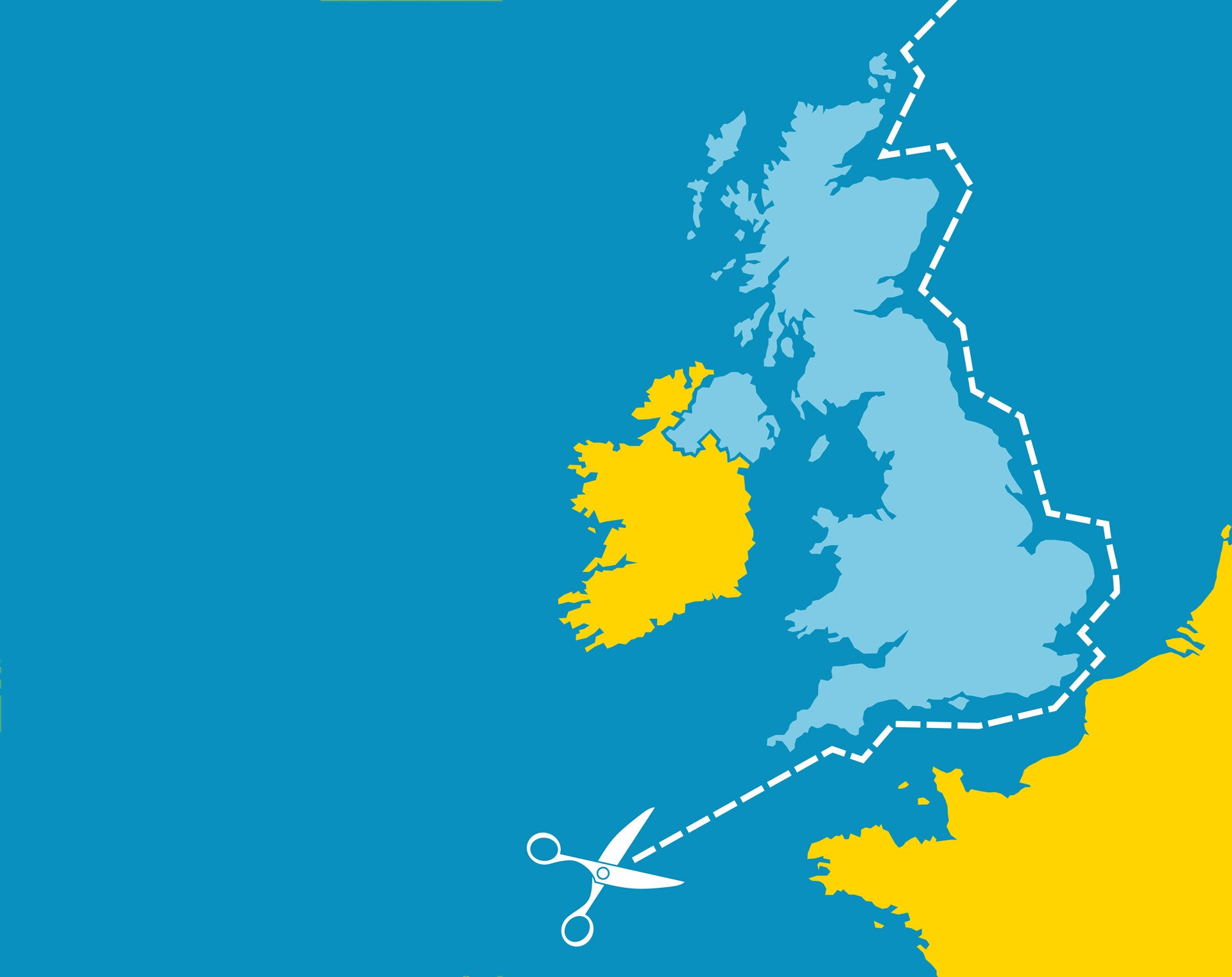
It’s been nearly three years since the UK voted to leave the European Union. Since then, a number of big multinationals have been planning for Brexit, with some – like Dyson, Nissan and Sony – choosing to move their European or global company headquarters overseas.
For smaller firms, the lack of clarity about the post-Brexit environment means many are adopting a ‘wait-and-see’ strategy. Others, however, are proactively investing in technologies that will give their business the agility required to cope with fast-evolving market scenarios.
There are some very specific challenges being banded around, so here we will aim to tackle some of the topics most discussed in relation to Brexit and manufacturing, and look at some of the steps that can be taken to mitigate their impact.
The reintroduction of the ‘Rules of Origin’ provision
The World Trade Organisation (WTO) Rules of Origin criteria are used by customs authorities to determine the economic nationality of a product. Once the origin of a product is established, the correct rate of duty or tariff can be applied to it when it crosses a border. Determining the country of origin of a product is usually the final step in the customer’s clearance process, once the customer’s classification and the value of the goods are known.
To date, the UK has benefited from the absence of origin requirements for trade within the EU. However, in the event of a hard Brexit, UK exporters will have to declare the origin of their goods when trading with the EU.
For process manufacturing companies in a variety of sectors – food and cars, computing and electronics, or anything that needs assembling – that means business is about to change.
How well do you really know your competitors?
Access the most comprehensive Company Profiles on the market, powered by GlobalData. Save hours of research. Gain competitive edge.
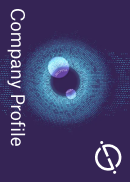
Thank you!
Your download email will arrive shortly
Not ready to buy yet? Download a free sample
We are confident about the unique quality of our Company Profiles. However, we want you to make the most beneficial decision for your business, so we offer a free sample that you can download by submitting the below form
By GlobalDataA new trading relationship with the EU means firms will need full traceability and visibility – and software that enables this – of their day-to-day operations. To ensure that compliance with complex country of origin rules can be demonstrated and assured when exporting to the EU, systems will need to handle more complexity than ever before in terms of the type of data held and frequency of submissions for customs declarations.
Brexit and manufacturing: Falling labour resources
As the flow of European workers slows ahead of Brexit, forward-thinking manufacturers are investing in automation and robotics as workers become more scarce and costly. Automating labour-intensive processes could generate major benefits for UK productivity, which currently lags more than 20% behind the US, France and Germany.
Modern enterprise resource planning (ERP) solutions will be crucial to coordinating robot workflows and enabling the sharing of data between machines and humans across multiple digital platforms. This, along with the addition of increased data processing efficiencies, and valuable real-time and data-driven insights, will allow manufacturers to navigate the murky Brexit waters, improve productivity and more easily drive future business growth.
Capturing data from production lines can also be used to undertake real-time monitoring of all activities, enhance process flows, and enable a more connected supply chain.
Supply chain disruption
Cross-channel goods could be reduced by 87% post-Brexit – which means the supply of components and raw materials manufacturers rely upon could be severely limited. Torn between planning for border gridlock caused by a no-deal Brexit, many manufacturers are said to be turning to stockpiling.
A recent survey found UK companies are ramping up their stockpiling efforts to ‘buffer’ operations against supply chain disruptions. As a result, UK warehouse space is nearing capacity, as manufacturers revert from ‘just-in-time’ (JIT) production models to ‘just-in-case’ models, in which high precautionary inventory levels are maintained.
While such contingency planning may help counteract potential supply chain disruptions on the horizon, it also increases the risk of waste or obsolescence – putting extra strain on already pressured firms.
Here, investment in supply chain management (SCM) software could help manufacturing companies to identify added-value activities, reduce and eliminate non-value-added activities, and move back towards a leaner and more efficient supply chain.
Made in Britain
The UK is synonymous with low-volume, high-quality, and high-value products. With trade tariffs predicted to squeeze margins, many UK manufacturers are looking to re-focus on near-shoring ‘Made in Britain’ manufacturing opportunities.
There are a number of reasons for bringing operations back to the UK or closer to home – rising overseas labour costs, modern slavery issues, maintaining control over operations and processes, and the positive brand benefits resulting from bringing jobs ‘home’.
Some firms have already realised the benefits of near-shoring versus off-shoring. One company extolling ‘Best of British’ virtues is PureMalt, a Scottish, family-owned manufacturer of innovative malt ingredients for the food and beverage industries that sources its materials within the UK. With a competitive, innovative product portfolio, and access to high-quality materials from Scotland and Northern England, PureMalt feels confident about overcoming the challenges that 2019 could bring.
Managing the supply chain for a changing world means management will need to have deep insights into how supply chain costs could change over the next five years while building up a new and trusted UK supplier base. Today’s modern ERP can make it easy to rebalance inventories and supply chains and make more informed decisions in real time.
The only certainty is, there will be more uncertainty
In these unpredictable times, modern ERP systems can enable manufacturers to respond to changes within the supply chain, adapt easily to new business models, and gain data-driven insights that inform decision-making and strategy.
To maintain – and increase – future manufacturing performance, manufacturing firms must be prepared to adapt to potential new regulations that could alter trade processes and possibly affect growth trajectories.
Today’s ERP systems make it easy to move to a leaner, paperless manufacturing environment, storing any document in a digital format and attaching this to any transaction, order or product item. With a few clicks, manufacturers can generate proof of origin documentation, maintain material planning information, manage compliance and control checks for international export rules, and more.
Similarly, they will need an ERP platform in place that makes it possible to take advantage of current and future advances, like robotic automation and digital technologies, to produce goods quickly and more efficiently. With the right ERP system in place, manufacturing firms can take advantage of IoT innovations and undertake real-time management of the connected factory floor. They’ll also gain real-time visibility into the entire supply chain to support lean-production strategies such as immediate ordering, fulfilment and delivery.
For UK manufacturers that need to create competitive advantage in today’s uncertain times, ERP systems not only serve to make businesses more responsive and agile. They can also provide the deep insights that make it possible to analyse the performance of contingency plans and identify which technical and organisational factors need to change to assure future growth.
Read more:Â UK tech industry holds its breath as Brexit hits crunch time