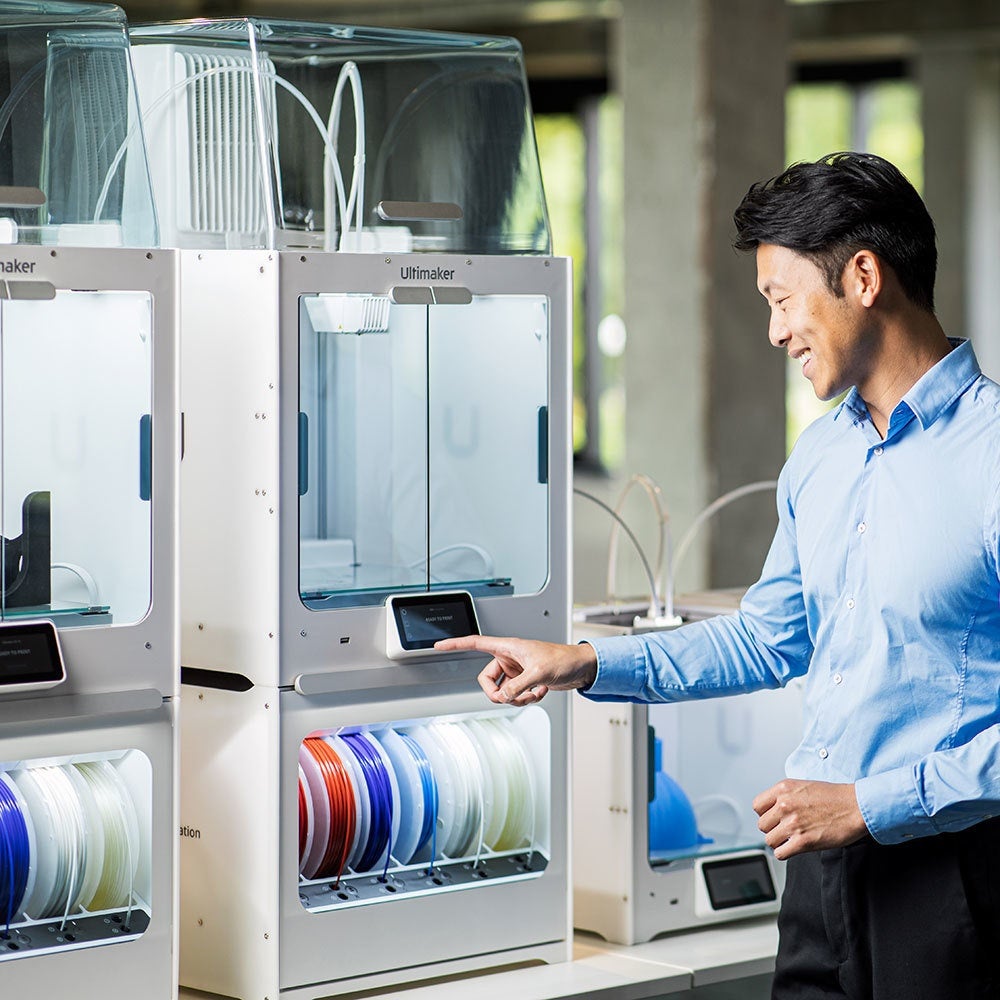
3D printing isn’t a vision of the future; it’s here now. However, with the growth of technologies such as artificial intelligence also competing to win the business of organisations across the globe, how do you make the business case for 3D printing?
The long-term capabilities of 3D printing, especially local print-on-demand solutions, have the potential to transform the supply chain. However, any company with additive manufacture can begin to explore the 3D printing journey to achieve incremental gains today.
Additive manufacturing: Working with existing methods
3D printing isn’t a replacement for traditional manufacturing processes, it’s a technology designed to complement and work alongside existing manufacturing methods too. As a case in point, print on demand spare parts can revolutionise uptime, especially in remote areas, enabling companies to cut down their transport and warehouse costs, reduce production downtime and optimise processes.
The accessibility of the complete 3D print solution model is now compelling. And the essential combination of hardware, software and materials maturity is now enabling organisations of every size to evaluate the potential use of 3D within a blended manufacturing model with a small, up-front investment.
The key question organisations are asking, however, is: where could 3D printing be explored to support essential business objectives?
Improving production uptime
Minimising production line downtime is at the top of every manufacturer’s agenda. As a crucial key performance indicator, improving uptime reduces costs, improves time to market and of course, supports strong customer relationships. However, despite how slick a companies production processes may be, failure of simple pieces of equipment can ultimately jeopardise uptime KPIs.
How well do you really know your competitors?
Access the most comprehensive Company Profiles on the market, powered by GlobalData. Save hours of research. Gain competitive edge.
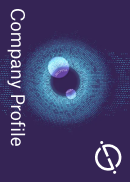
Thank you!
Your download email will arrive shortly
Not ready to buy yet? Download a free sample
We are confident about the unique quality of our Company Profiles. However, we want you to make the most beneficial decision for your business, so we offer a free sample that you can download by submitting the below form
By GlobalDataFor automotive manufacturer Volkswagen Autoeuropa, 3D printing is delivering new levels of control over the supply chain, manufacturing aids that are used daily on an assembly line that produces 100,000 vehicles a year. By removing reliance on external suppliers for tools, jigs and fixtures, the company has reduced costs and lead times from weeks to just days.
Enhancing function and performance
3D printing enables companies to create highly complex designs and make rapid revisions and amendments, without cost penalties or long lead times. The tools can be tailored to match exact requirements, making function and performance the main drivers of design rather than cost or time.
For example, a new tool can be printed overnight, and the next morning it is tested on the assembly line by the operators. This feedback can then be used to inform future designs until the perfect tool for the job is created.
Looking after employees
A great benefit of 3D printing is the health and safety aspect. As an example, 3D printed plastic tools or guides are far easier to work with than traditional rough metal tools. Indeed, the iterative nature of Additive Manufacturing enables organisations to continually improve the usability of such equipment, transforming worker experience, which consequently affects wellbeing and may lead to a boost in morale amongst teams.
The speed with which 3D innovations can be expanded across businesses is also important. Parts can be sent digitally rather than physically, providing vital solutions in areas that struggle with poor transport links.
Heineken, for example, is using this technology to localise part of their production process in Africa, where they see challenging lead times for parts. By printing these parts in or close to the breweries, they are able to avoid global shipping, improve control and uptime while ensuring safety features are also deployed globally.
The business case for 3D printing
By focusing 3D printing on the key business objectives, whether it is improving health and safety, transforming uptime or reducing reliance on third party suppliers to minimise risk, the business case is robust.
However, the challenge amongst many organisations is that despite the awareness of 3D printing across a number of industries, organisations remain perplexed as to how to move forward.
Confidence will come from selecting the right kit with a low technical threshold, as well as accessing the right materials, exploring the right software interfaces from design to preparation and, critically, choosing to work with people who are willing to offer their support and knowledge where necessary.
Read more: The future of 3D printing is all about materials