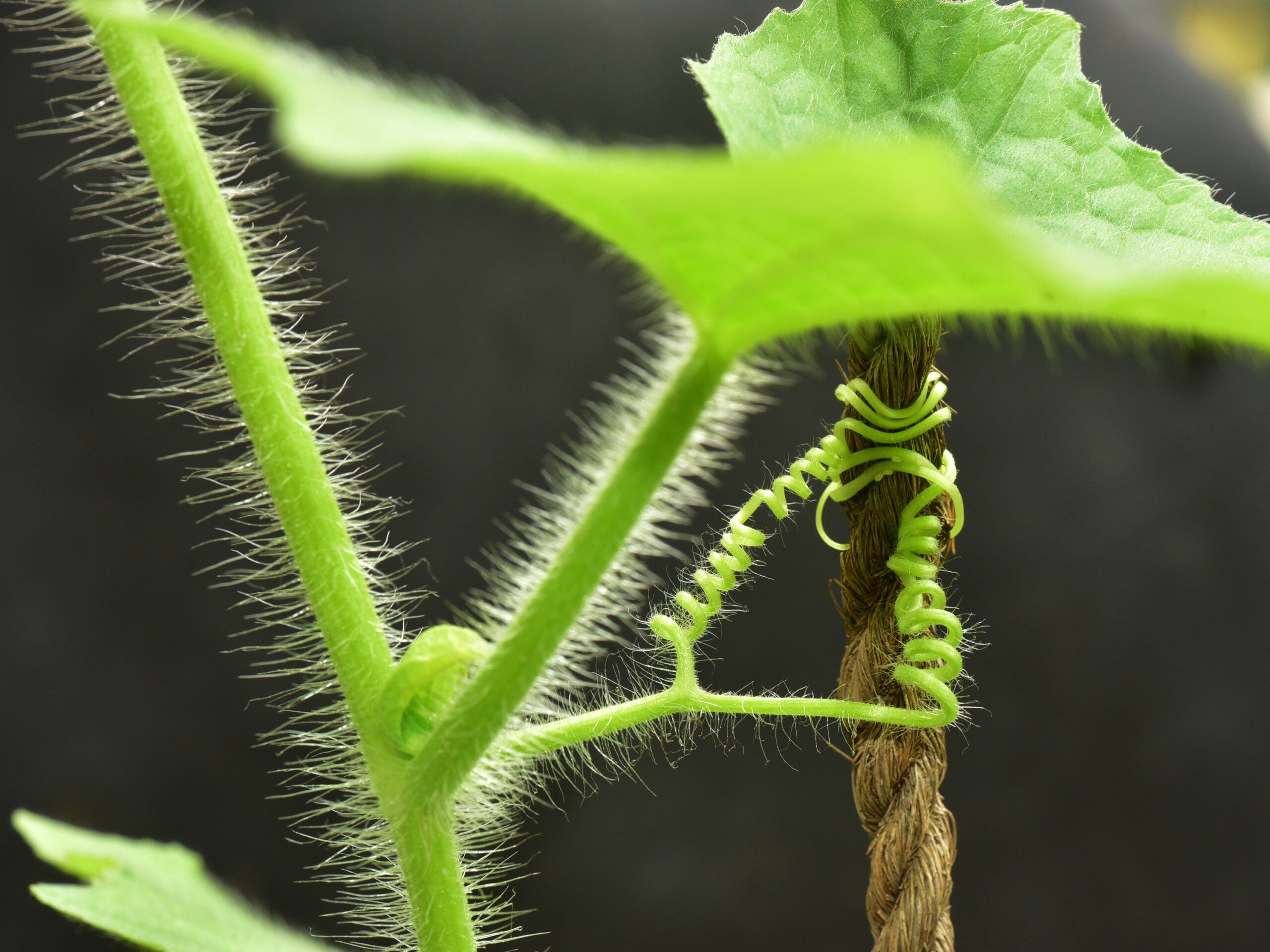
US researchers have created ‘artificial muscles’ that imitate the coiling and pulling mechanism found in a cucumber plant’s tendrils.
The artificial muscles consist of coil-shaped fibres made from two polymers. The fibre coil reacts to heat by tightening up, producing a strong pulling force. When cooled down, the fibre returns to its original length.
The Massachusetts Institute of Technology (MIT) researchers who developed the technology say a single fibre can lift 650 times its own weight.
The technology underpinning the artificial muscles could be used in robots, prosthetic limbs or other mechanical and biomedical applications.
Fibres can be made in different sizes, from millimetres to micrometres in width meaning it could also be used for smaller-sized robots.
“Such fibres might also find uses in tiny biomedical devices, such as a medical robot that works by going into an artery and then being activated,” said MIT professor Polina Anikeeva. “We have activation times on the order of tens of milliseconds to seconds,” depending on the dimensions, she added.
How well do you really know your competitors?
Access the most comprehensive Company Profiles on the market, powered by GlobalData. Save hours of research. Gain competitive edge.
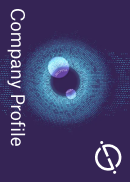
Thank you!
Your download email will arrive shortly
Not ready to buy yet? Download a free sample
We are confident about the unique quality of our Company Profiles. However, we want you to make the most beneficial decision for your business, so we offer a free sample that you can download by submitting the below form
By GlobalDataResearchers created the fibres by combining two polymers: the stretchable cyclic copolymer elastomer and the stiffer thermoplastic polyethylene.
MIT postdoctoral student Mehmet Kanik realised the potential of the material after he picked it up for the first time and the coil curled more tightly from the heat from his hand alone.
10,000 reps and still going strong
The researchers say the fibres could be bundled together to lift heavier loads in a similar way that muscle fibres are in the body.
Their tests used meshes of conductive nanowires that acted as sensors and measured the tension in the fibre.
They found that the contracting and expanding could be repeated 10,000 times “and it was still going strong,” said Anikeeva.
She added that this longevity is possible because of the moderate conditions that it operates under, which means the artificial muscle is under less stress than it would be under high heats to activate it.
The nanowire mesh could one day include heating elements such as electrodes to activate the muscle without applying heat externally.
Previous methods for making artificial muscles include hydraulic systems, servo motors, shape-memory metals and polymers that respond to stimuli. However, these all have their own limitations, including slow response times and heavy weights.
The team said the new technology is extremely lightweight and offers a shorter response time.
“The strength of this work is coming from its simplicity,” said Kanik.
The findings were published yesterday in the journal Science
Read more: 3D printed prosthetic leg socket tracks calories burnt in style