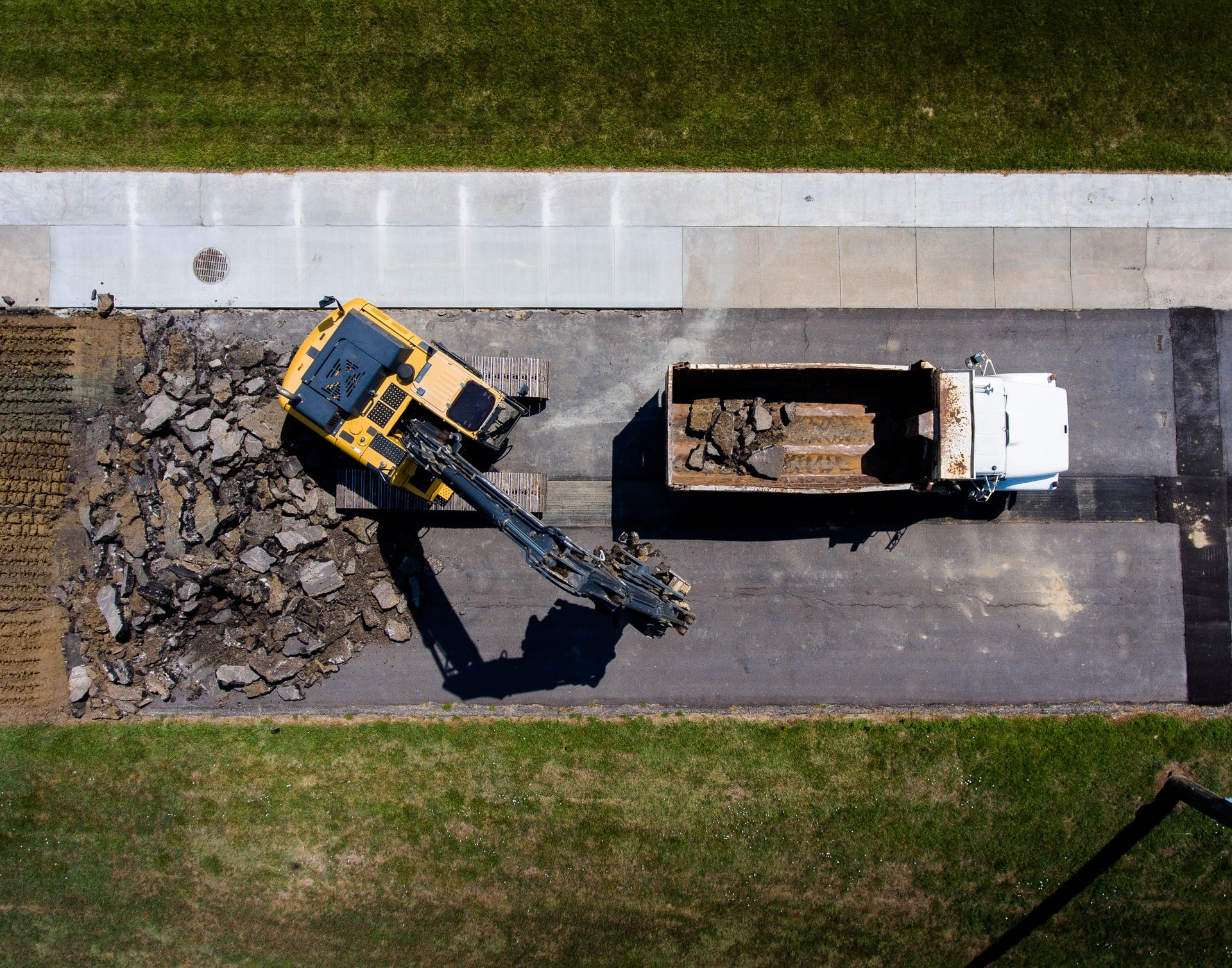
In 2019, construction contributed 6% of the UK’s gross domestic product and employed 2.4 million people – 6.6% of the entire workforce. However, the sector’s immense size and importance belies a core problem: low productivity. The Office for National Statistics estimates that average output in the construction sector stands at £29.40 per hour, compared to the national average of £36.50, and is roughly 25% lower than the average across manufacturing.
One of the major reasons for construction’s productivity problem is that globally, the sector is recognised as one of the least digitalised industries. This is an assessment shared by the sector itself. A recent survey of 200 key decision-makers across the UK building industry found that 54% felt that the industry had been slow to adopt new technologies.
Given the benefits that digitalisation has brought to other sectors, what is holding construction back? We can identify three major reasons: the large capital investment traditionally required for digitalisation, the complexity of the industry, and the difficulty in securing buy-in for digitalisation with a wide variety of stakeholders.
Why construction is behind in digitalisation
One of the primary reasons for construction’s digitalisation deficit is that it’s hard for building firms to afford the initial investment. Digitalisation projects have traditionally meant large, organisation-wide efforts to overhaul technology and processes, which means a significant capital expenditure. In a low margin environment, such as construction, this sort of capital-intensive model for digitalisation is difficult to embrace. In the aforementioned survey of key decision-makers, 56% believed that low margins had restricted their ability to invest in new technology.
A second reason for construction’s digitalisation deficit is the sheer complexity of the industry. Construction projects see lots of stakeholders involved in every stage of proceedings, including clients, employees, contractors, developers, architects, suppliers and consultants. This makes it difficult to standardise and digitalise processes, and such a crowded and multifarious prospective user base is difficult to onboard.
There are also issues with connectivity. Compared to a white-collar worker at a desk or even a factory worker on an assembly line, it’s much harder to utilise technology that tracks, analyses, and improves processes in an industry where day-to-day labour is highly mobile and where the work environment itself rapidly changes over time.
How well do you really know your competitors?
Access the most comprehensive Company Profiles on the market, powered by GlobalData. Save hours of research. Gain competitive edge.
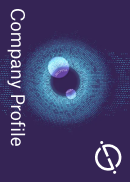
Thank you!
Your download email will arrive shortly
Not ready to buy yet? Download a free sample
We are confident about the unique quality of our Company Profiles. However, we want you to make the most beneficial decision for your business, so we offer a free sample that you can download by submitting the below form
By GlobalDataA third reason why construction lags in digitalisation is hesitancy from workers themselves. Construction unions and many workers are concerned about digital technologies encroaching on worker privacy and autonomy through logging their activity. This makes buy-in for new technologies very difficult, especially when they don’t provide any immediate benefit on the ground and seemingly just add additional work and sources of supervision to their jobs.
However, these reasons should not be seen as evidence that construction is not a viable space for digitalisation in the first place. Rather, it shows that digitalisation in the sector requires a different approach – aiming for iterative improvement rather than a total overhaul. This is where construction tech startups become vital.
How the iterative approach of startups changes the dynamic
When it comes to investing in technology, then, the low margins of the construction industry are a major bottleneck. In the absence of debt financing, traditional digitalisation projects in the sector would require a long period of saving prior to investment – all with a high degree of uncertainty as to whether that investment would pay off.
Startups offering construction tech solutions offer a challenge to this paradigm. This is because a startup’s approach to digitalisation is modest in its approach. Rather than seeking to digitalise an entire organisation’s IT infrastructure at once, startups have thrived on optimising specific challenging processes and then creating APIs to allow their platforms to integrate into other systems. This changes digitalisation from a monolithic process to an iterative one, which is much more amenable to low-margin businesses.
In addition, startups typically monetise by offering digital transformation as an operational expense rather than a capital expense. That is, a subscription rather than an investment. This works particularly well with low-margin organisations, since it means they don’t have to spend a long time accumulating and risking a large investment. Instead, the operational expense model of startups lets them test solutions and build the ongoing costs into their business plans.
Construction startups: Digitalising to solve specific problems
In addition to affordability, collaborating with tech startups means that workers and stakeholders can tackle specific problems with tangible solutions, as opposed to a wider overarching digital transformation project. Unlike top-down digitalisation initiatives, startups are invested in ensuring that their solutions identify and fix particular pain points that are close to the users themselves. This means that a digital tool that provides immediate relief to a pain point will quickly find a willingness to be used by teams.
Startups can focus on optimising particular processes, concentrating on the granular and low-level, and they also have room to run pilot projects to see what works and what doesn’t for users on the ground. Through using APIs and other integration tools, construction firms can then seamlessly fit individual digitalised processes together.
Rather than being a sudden switch, startups present a new path to digitalisation for the building industry by allowing firms to iterate and test processes to make financial and practical sense in their relevant context. Through providing specific and clear services that optimise processes one by one, construction tech startups make digitalisation financially viable, operationally sound, and aligned with the interests of workers and other stakeholders.
Marie-Helene Ametsreiter is industrial tech lead partner at Speedinvest, a venture capital fund that invests in seed & early-